CNC Machining Service
- Ideal for prototyping and small batch machining
- Prices significantly lower than those of competitors
- Quality machining in China with verified partners
- Perfect for non-urgent projects, while providing substantial savings.
- Certification and Inspection Report on request
The advantages of CNC Machining
CNC Machining on Demand
Materials, Precision and Finishes
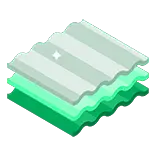
Wide Choice of Materials
L'usinage CNC offre une grande flexibilité dans le choix des matériaux, allant des métaux (aluminium, acier inoxydable, laiton) aux plastiques techniques (ABS, POM, PTFE). Cela permet de répondre à des besoins variés, que ce soit pour des pièces résistantes, légères ou spécifiques à des applications industrielles.
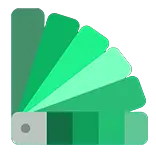
Custom Finishes
With CNC machining, you can achieve customised finishes, ranging from raw machining to surface treatments such as anodising, polishing, or powder coating. These options ensure ready-to-use parts that meet specific aesthetic or functional requirements.
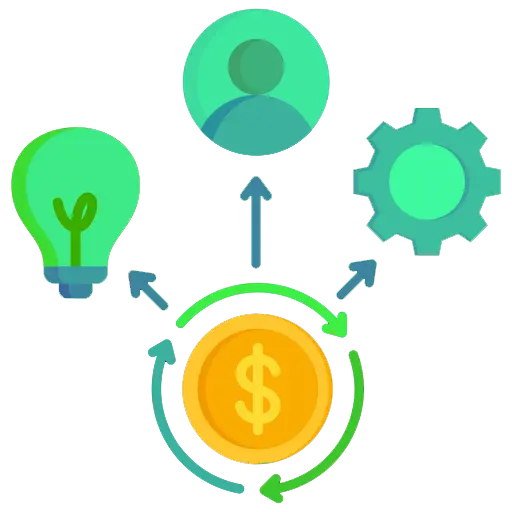
Execution Speed with Optimised Delay
Even though the average lead times are between 15 to 25 days depending on the quantities and the complexity of the parts, CNC machining allows for the production of complex components within a reasonable timeframe. This ensures a perfect balance between competitive prices and delivery times suited to non-urgent projects.
Economic and Flexible Production
Small Series and Prototyping
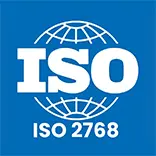
ISO 2768 Standard Precision
CNC machining allows for exceptional precision, often standardised according to ISO2768. This ensures tight tolerances, reproducibility, and perfect accuracy, ideal for sectors requiring high-quality technical parts.
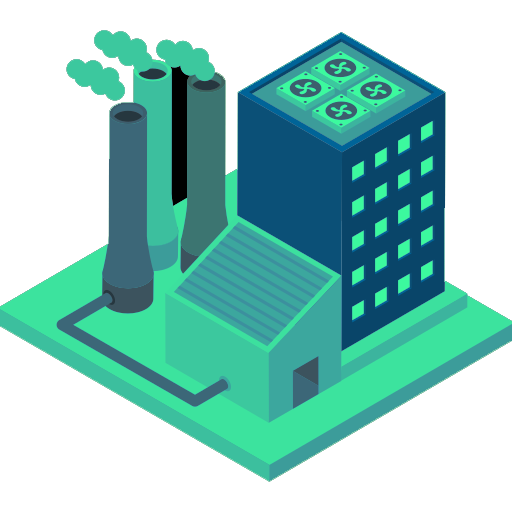
Flexibility for Small Batches and Prototyping
Thanks to its ability to quickly produce parts, CNC machining is particularly suited for small batches and prototypes. You can test and adjust designs with great responsiveness, while keeping costs under control, without the constraints of traditional manufacturing methods.
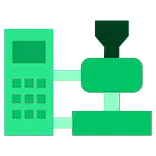
Cost Reduction through Automation
The complete automation of the CNC machining process helps to reduce labour costs and human errors. This optimised process is particularly beneficial for clients seeking cost-effective solutions without sacrificing quality.
How to use our CNC machining services?
From the development of the prototype to small-scale production.
Send us your CAD files
Use our form to customise your choices and request a quote.
Feasibility study
We analyse your CAD files with our collaborators and will conduct a feasibility study.
Order your parts
A quote will be sent to your email address. You will be able to view your quote requests directly on your online account.
Receive your parts
We manufacture and inspect your parts. At the end of the manufacturing process, the parts undergo quality control.
CNC Machining Materials
Aluminium 2007 / 3.1645 / Al-CuMgPb - High machinability for precision components.
Aluminium 2011 / 3.1655 / Al-CuBiPb - Easy machining and finishing for complex parts.
Aluminium 2024 / 3.1355 / Al-Cu4Mg1 - High tensile strength for aerospace components.
Aluminium 5083 / 3.3547 / Al-Mg4.5Mn0.7 - Corrosion resistance for marine applications.
Aluminium 5754 / 3.3535 / Al-Mg3 - Lightweight structures and tanks with good corrosion resistance.
Aluminium 6060 / 3.3206 / Al-MgSi - Lightweight profiles and structures with good corrosion resistance.
Aluminium 6061 / 3.3211 / Al-Mg1SiCu - Machine components requiring high strength.
Aluminium 6082 / 3.2315 / Al-Si1MgMn - Structural applications with high mechanical strength.
Aluminium 7075 / 3.4365 / Al-Zn6MgCu - Aerospace components with high strength and rigidity.
Aluminium 5086 / 3.3545 / Al-Mg4 - Marine applications requiring excellent corrosion resistance.
Steel 1.0038 / S235JR – General applications and steel structures with good weldability.
Steel 1.0577 / C45 – Mechanical components requiring high tensile strength.
Steel 1.1191 / S355J2 - Heavy structures and parts requiring high strength.
Acier 1.4301 / X5CrNi18-10 – Applications en inox pour résistance à la corrosion et à la chaleur.
Acier 1.4541 / X6CrNiTi18-10 – Applications haute température et résistance à la corrosion dans des environnements agressifs.
Acier 1.7225 / 42CrMo4 – Composants soumis à des charges élevées nécessitant une bonne résistance à l'usure.
Acier 1.2083 / X40Cr14 – Composants de moules avec une bonne résistance à l’usure et à la corrosion.
Acier 1.2714 / H13 – Outils de formage et applications nécessitant une résistance à la chaleur et à l'usure.
Acier 1.7131 / 16MnCr5 – Composants mécaniques nécessitant une bonne résistance à la fatigue et à l’usure.
Acier 1.2631 / 42CrMoS4 – Composants de haute performance avec une bonne résistance à la fatigue et à l’usure.
Stainless steel 1.4301 / X5CrNi18-10 / 304 – General applications for good resistance to corrosion and heat.
Stainless steel 1.4541 / X6CrNiTi18-10 / 321 – High temperature applications with increased resistance to corrosion and aggressive environments.
Stainless steel 1.4401 / X5CrNiMo17-12-2 / 316 – Corrosive environments and marine applications requiring high corrosion resistance.
Stainless steel 1.4462 / X2CrNiMoN22-5-3 / 2205 – Marine and industrial applications with excellent resistance to corrosion and wear.
Stainless steel 1.4307 / X2CrNi18-9 / 304L – Food components and applications with good resistance to mild corrosion.
Stainless steel 1.4539 / X1NiCrMoCu25-20-5 / 904L – Chemical environments and applications requiring increased resistance to acids.
Stainless steel 1.4841 / X15CrNiSi25-21 / 309 – High-temperature applications requiring good oxidation resistance.
Stainless steel 1.4410 / X4CrNiMo16-5-1 / 2507 – Industrial applications with high resistance to corrosion and fatigue.
Stainless steel 1.4501 / X4CrNiCuNb16-3 / 825 – Applications in highly corrosive environments with increased wear resistance.
Stainless steel 1.4418 / X2CrNiMo18-14-3 / 316Ti – High-performance components requiring corrosion resistance and good mechanical strength.
Copper C11000 / Cu-ETP – Electrical applications requiring high conductivity and good machinability.
Copper C36000 / Cu-Zn39Pb3 – Machined parts with excellent machinability and wear resistance.
Copper C19400 / Cu-Cr-Zr – High-performance components with high mechanical strength and conductivity.
Copper C70250 / Cu-NiSi – Marine applications with increased corrosion resistance and good machinability.
Copper C10600 / Cu-T1 – Architectural applications with good corrosion resistance and ease of forming.
Copper C28000 / Cu-Zn15 – Plumbing applications with good resistance to corrosion and wear.
Copper C10200 / Cu-OFE – Electronic applications with high purity and excellent conductivity.
Brass CW614N / CuZn39Pb3 – Machined parts with excellent machinability and wear resistance.
Brass C37700 / CuZn40Pb2 – Plumbing applications and precision parts with good corrosion resistance.
Brass C36000 / CuZn39Pb3 – Mechanical components requiring high machinability and wear resistance.
Copper alloy C28000 / CuZn15 – Foundry applications with good wear resistance and ease of machining.
C26100 Brass / CuZn30 – Decorative applications with good corrosion resistance and good machinability.
Brass C26800 / CuZn28 – Industrial applications with good corrosion resistance and ease of machining.
Titanium Grade 2 / Ti-Grade 2 – General applications requiring good corrosion resistance and excellent formability.
Titanium Grade 5 / Ti-6Al-4V – High-performance applications with high mechanical strength and good corrosion resistance.
Titanium Grade 6 / Ti-6Al-4V ELI – Medical and aerospace applications requiring better ductility and strength.
Titanium Grade 7 / Ti-0.2Pd – Chemical applications with enhanced corrosion resistance in aggressive environments.
Titanium Grade 9 / Ti-3Al-2.5V – Applications in sports and high performance with a good balance between strength and weight.
Acetal (POM) / Delrin – Mechanical applications requiring good machinability, wear resistance, and low friction.
Nylon (PA) / Polyamide – Industrial applications with good impact resistance, machinability, and moisture resistance.
Polycarbonate (PC) / Lexan – Optical and mechanical applications requiring good impact resistance and clarity.
Acrylonitrile Butadiene Styrene (ABS) / ABS – Various applications requiring good impact resistance and ease of machining.
Polytetrafluoroethylene (PTFE) / Teflon – Chemical applications requiring excellent heat and corrosion resistance.
Polyethylene (PE) / HDPE – Applications for containers and piping with good impact resistance and machinability.
Methyl methacrylate (PMMA) / Plexiglass – Transparent applications requiring good optical clarity and machinability.
Polyetheretherketone (PEEK) / PEEK – High-temperature applications requiring enhanced resistance to heat and chemicals.